Filament-extrusion
Entdecken Sie unsere herausragende Entwicklung: GalloPP GF25, ein Polypropylen Filament mit einem Glasfaseranteil von 25%. Wir sind Ihr verlässlicher Partner für hochwertige Filamente und maßgeschneiderte Filamentrezepturen in der Welt der Kunststoffextrusion.
Filamentextrusion
Die Filamentextrusion ist ein grundlegender Prozess in der 3D-Drucktechnologie, bei dem Kunststofffilamente hergestellt werden. Diese hochwertigen Filamente werden anschließend in 3D-Druckern verwendet, um Objekte Schicht zu Schicht zum Leben zu erwecken. Dieser Prozess eröffnet eine vielfältige Palette von Kunststoffmaterialien für den 3D-Druck und damit grenzenlose Anwendungsmöglichkeiten.
Unsere Leidenschaft für die Filamentextrusion treibt uns an, innovative Lösungen für Ihre individuellen Bedürfnisse zu entwickeln. Egal, ob Sie hochwertiges Filament suchen oder Ihre eigenen Filamentrezepturen kreieren möchten, wir sind Ihr verlässlicher Partner in der Welt der Kunststoffextrusion.
GalloPP GF25
Unser eigens entwickeltes Filament für den 3D-Druck besteht aus modifiziertem Polypropylen mit 25% Glasfaseranteil. Das Ergebnis? Minimale Schwindung und Warping, ausgezeichnete Haftung und präzise Druckergebnisse aufgrund einer bemerkenswerten Dimensionsstabilität – ganz ohne spezielle Druckplatte!
GalloPP GF25 zeichnet sich durch seine hohe Schlagzähigkeit, Flexibilität und Säurebeständigkeit aus, was es ideal für aggressive Umgebungen macht. Es ist witterungs- und UV-beständig und somit bestens für den Außeneinsatz geeignet. Die matte, raue Oberfläche sorgt für ansprechende Drucke, wobei bei kritischen Stellen eine zusätzliche Materialdimensionierung empfohlen wird. Dank seiner Vielseitigkeit eignet es sich sowohl für Innen- als auch Außeneinsätze jeglicher Art.
Zu den Vorteilen zählen eine einfache Prozessführung ohne beheizten Bauraum, chemische Beständigkeit gegenüber Salzlösungen, Säuren und Alkalien sowie eine hohe Einsatztemperatur von 100°C bis 140°C. Zudem ist die Lagerung durch die geringe Feuchtigkeitsaufnahme unkompliziert.
Unser Produkt wird bei Würzburg, Deutschland, hergestellt und steht für Qualität „Made in Germany“.
Für weiterführende Informationen zu den technischen Eigenschaften sowie sicherheitsrelevanten Hinweisen stellen wir Ihnen gerne das technische Datenblatt und das Sicherheitsdatenblatt zur Verfügung. Die entsprechenden Dokumente sind für Sie nachfolgend verlinkt:
Unsere Farbpalette
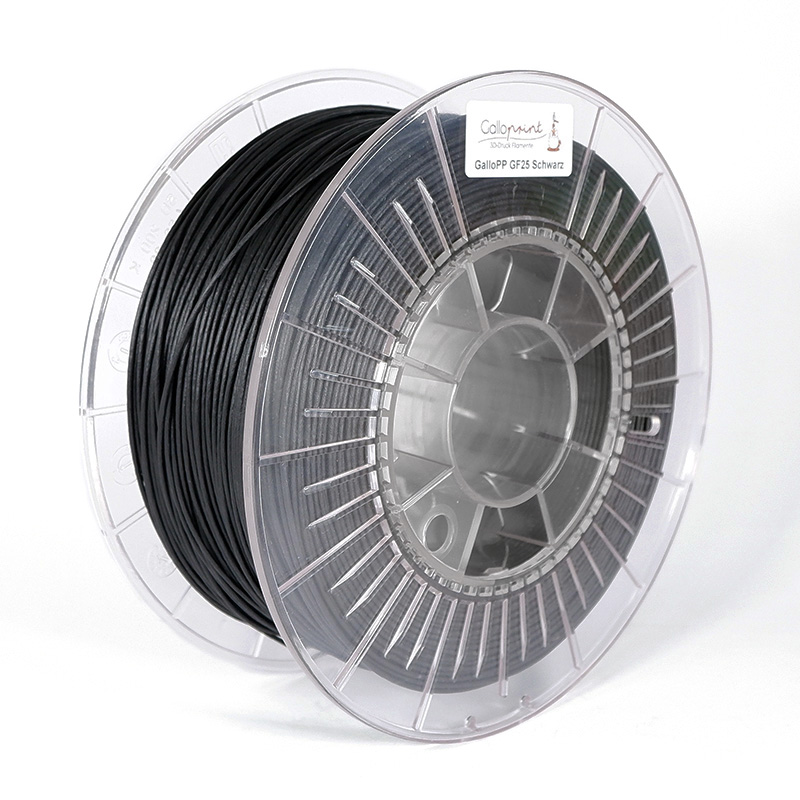
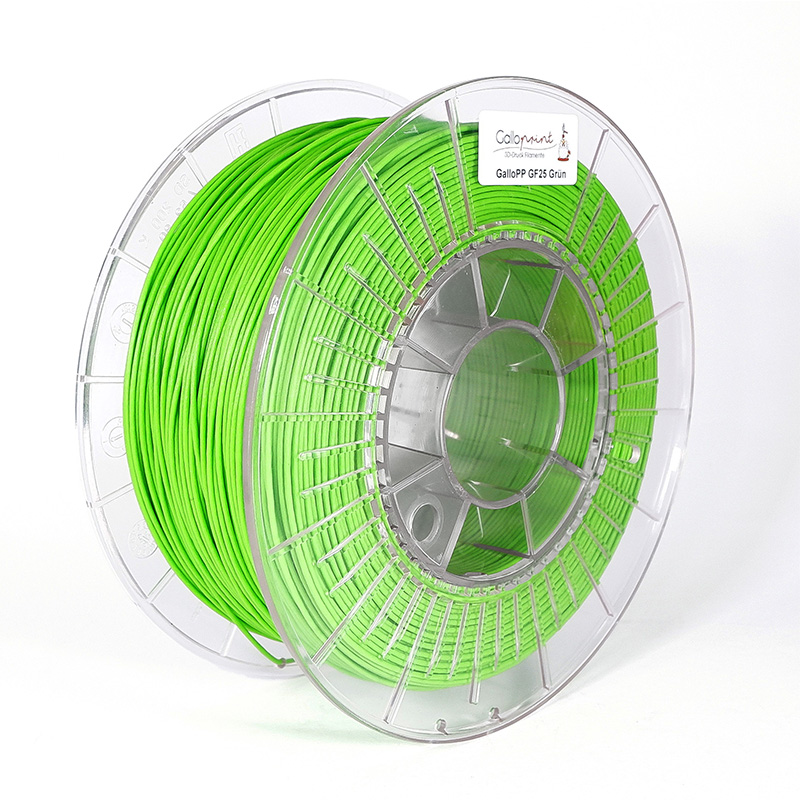
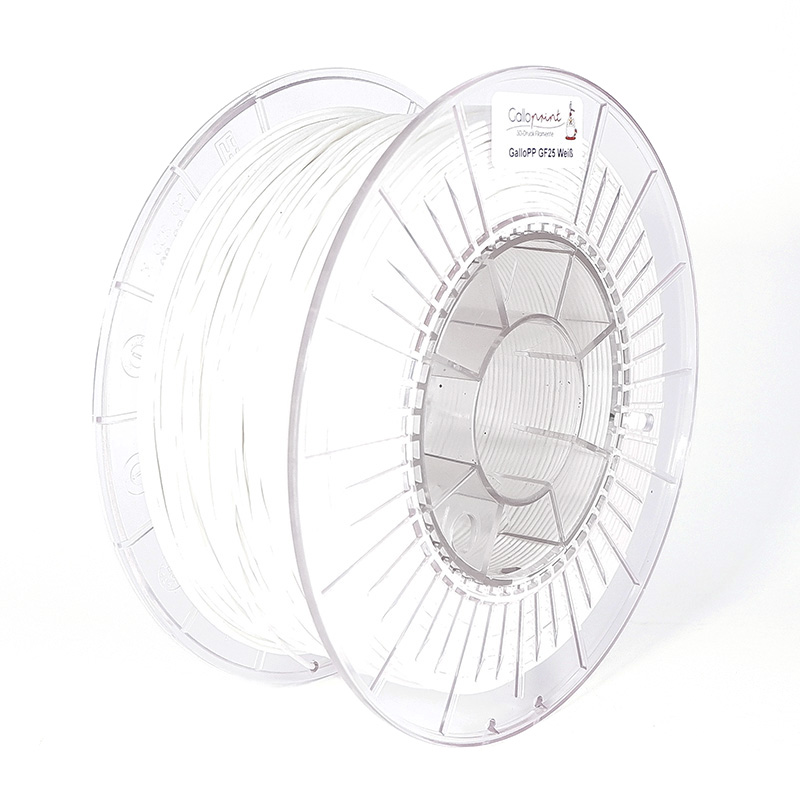
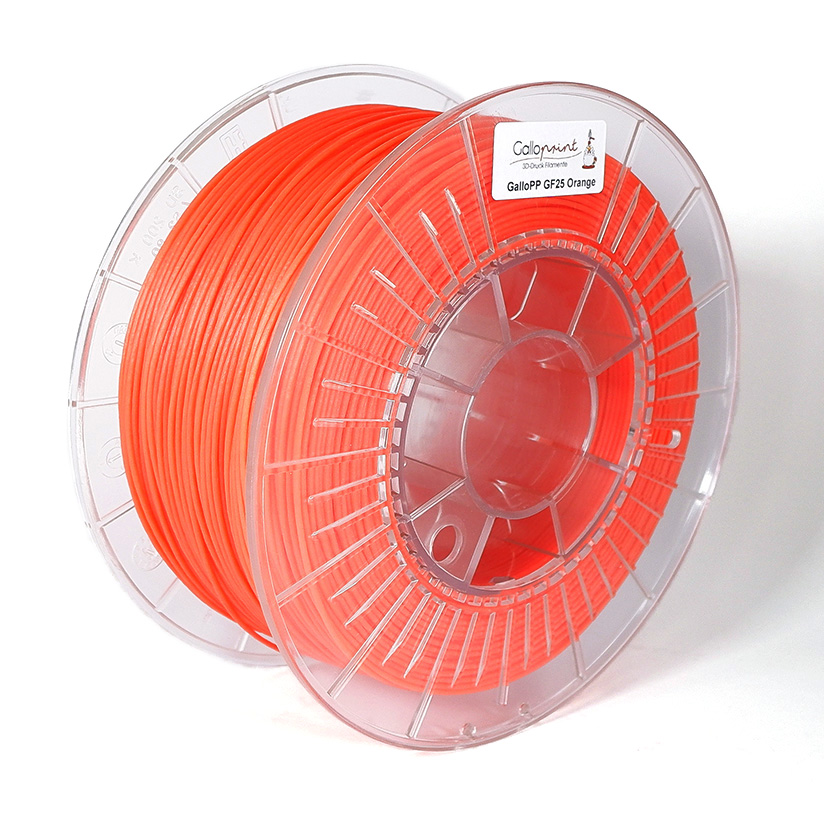
Kontaktieren Sie uns noch heute
Falls Sie weitere Informationen benötigen, sind wir gerne für Sie da und unterstützen Sie mit Freude. Wir freuen uns darauf, von Ihnen zu hören!
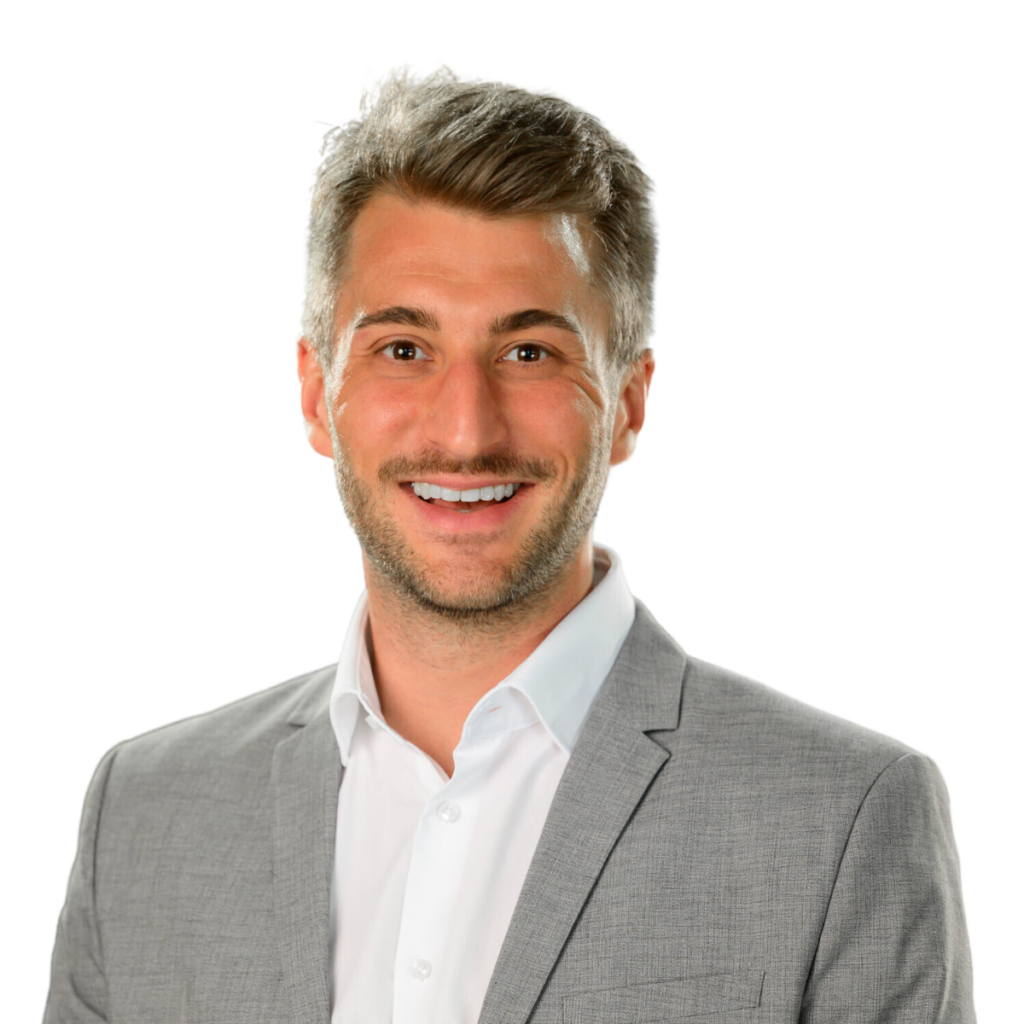
Unsere Dienstleistungen umfassen:
Filamentextrusion: Unser hochqualifiziertes Team und modernste Extrusionsanlagen ermöglichen uns die Herstellung von Filament in verschiedenen Materialien. Wir garantieren Ihnen Filamente höchster Qualität, die den strengsten Industriestandards entsprechen.
Kundenspezifische Filamententwicklung: Sie haben eine spezielle Anforderung oder eine einzigartige Filamentrezeptur im Sinn? Wir arbeiten eng mit Ihnen zusammen, um maßgeschneiderte Filamente zu entwickeln, die Ihren Anforderungen gerecht werden.
Qualitätskontrolle: Wir legen großen Wert auf Qualität und überwachen den gesamten Herstellungsprozess sorgfältig. Jedes Filament wird strengen Qualitätskontrollen unterzogen, um sicherzustellen, dass es den höchsten Standards entspricht.
Nachhaltigkeit: Wir setzen uns für umweltfreundliche Produktionsverfahren ein und bieten umweltfreundliche Filamentoptionen an. Gemeinsam können wir die Umweltauswirkungen Ihres Projekts minimieren.
Kundenservice: Unsere Kunden stehen im Mittelpunkt unseres Unternehmens. Wir sind stolz auf unseren exzellenten Kundenservice und stehen Ihnen bei Fragen oder Anliegen gerne zur Verfügung.
Wir verstehen, dass Filament ein entscheidender Bestandteil Ihres 3D-Druckprozesses ist, und wir sind bestrebt, Ihnen die bestmöglichen Lösungen zu bieten. Unser Engagement für Qualität, Innovation und Nachhaltigkeit macht uns zum idealen Partner für Ihre Filamentbedürfnisse.
Kontaktieren Sie uns noch heute, um mehr über unsere Dienstleistungen zu erfahren und wie wir Ihnen bei der Herstellung hochwertigen Filaments behilflich sein können. Wir freuen uns darauf, mit Ihnen zusammenzuarbeiten und Ihre Ideen in die Realität umzusetzen.